На підприємствах чорної металургії та відходять технологічними газами і вентиляційним повітрям несеться велика кількість токсичних твердих і газоподібних речовин, що забруднюють навколишнє середовище. Модернізація діючих і встановлення нових аспіраційних систем на всіх стадіях виробництва - важлива екологічна завдання вітчизняних металургійних заводів.
Джерела утворення
Найбільшим джерелом забруднення навколишнього середовища в чорній металургії є агломераційне виробництво. Аглофабрики викидають в атмосферу близько 50% всієї кількості оксиду вуглецю (СО) і сірчистого ангідриду (SO2), понад 20% оксидів азоту (NOх) і пилу. Під час агломерації руди відбувається вигоряння сірки з піритів. Сульфідні руди містять до 10% сірки, а після агломерації її залишається лише 0,2-0,8%. В середньому, одна стрічкова машина дає близько 700 т сірчистого газу на добу.
Іншим значним джерелом забруднень залишається доменне виробництво, викидає близько 30% всього пилу, 25% - СО, 15% - SO2, 10% - NOх. Пил і газоподібні викиди з доменних печей утворюються в результаті складних фізичних і хімічних процесів. Вважається, що з доменним газом з печі виносяться пил, внесена з шихтою і пил, що з`явилася при терті стовпа шихти в самій доменної печі. Маса пилу, що виноситься з доменними газами, становить 20-100 кг / т чавуну.
Пиловиділення з печі обумовлено тим, що при подачі шихти на великий конус завантажувального пристрою печі тиск по обидва боки конуса необхідно вирівняти, для чого неочищений газ з міжконусного простору виводять в атмосферу. Запиленість газу під час вихлопу становить 250-700 г / куб. м. Питома викид пилу досягає 4 кг на 1 т чавуну при основному режимі роботи печі. Крім того, пиловиділення відбувається при кожному зсипання скіпа до приймальні воронку.
Крім колошникового пристрою доменної печі, джерелом забруднення атмосфери доменного цеху є рудний і ливарний двори. На рудному дворі пил виділяється при розвантаженні вагонів, перевантаження руди, подачі руди на бункерну естакаду і т.д. Питомий виділення пилу на рудному дворі складає приблизно 50 кг на 1 т чавуну, а на бункерній естакаді - 20 кг на 1 т чавуну. Концентрація пилу на рудному дворі і бункерній естакаді коливається від 17 до 1000 мг / куб. м. На ливарному дворі пил і гази виділяються, в основному, від льоток чавуну і шлаку, жолобів ділянок зливу і ковшів. Питомі виходи шкідливих речовин на 1 т чавуну складають: 400-700 г пилу, 700-1150 г СО, 120-170 г SO2. Максимальна кількість пилу і газів викидається під час випуску чавуну і шлаку.
Не останню роль у забрудненні атмосфери грають викиди мартенівських і конвертерних сталеплавильних цехів. При веденні мартенівського процесу пил утворюється з металевої шихти, з шлаку, руди, вапняку і окалини, що йдуть на окислення домішок шихти, з доломіту, що застосовується для заправки пода печі. При кипінні стали виділяються пари окислів шлаку та металу, гази. Розміри частинок пилу не перевищують 3 мкм. При бескислородном процесі на 1 т мартенівської сталі виділяється 3000-4000 куб. м газів з концентрацією пилу в середньому 0.5 г / куб. м. У період подачі кисню в зону розплавленого металу пилоутворення багаторазово збільшується, досягаючи 15-52 г / куб. м.
Крім того, плавлення сталі супроводжується вигорянням деякої кількості вуглецю і сірки, у зв`язку з чим в відведених газах мартенівських печей при кисневому дуття міститься до 60 кг окису вуглецю і до 3 кг сірчистого газу в розрахунку на 1 т видається сталі. При конвертерному способі отримання сталі утворюються димові гази з частинок оксидів кремнію, марганцю і фосфору. У складі диму міститься значна кількість окису вуглецю - до 80%. Концентрація пилу в газах становить приблизно 15 г / куб. м. Основна маса пилу (близько 90%) складається з частинок розміром 0.2-1 мкм.
Коксохімічні виробництва також забруднюють атмосферне повітря пилом і сумішшю летючих з`єднань. При коксуванні 1 т вугілля утворюється 300-320 куб. м коксового газу. До його складу входять водень, метан, окис вуглецю, вуглекислий азот, азот, вуглеводні і кисень. Основна маса коксового газу вловлюється і направляється на хімічну переробку та утилізацію, але близько 6% газу надходить в атмосферу внаслідок втрат під час завантаження і вивантаження печей і негерметичності апаратури. Забруднення повітря пилом при коксуванні вугілля пов`язане з підготовкою шихти та завантаженням її в коксові печі, з розвантаженням в гасильних вагони і мокрим гасінням коксу. Мокре гасіння супроводжується також викидом в атмосферу речовин, що входять до складу використовуваної води.
Види пилоуловлювачів
Для уловлювання пилу і газів, що потрапляють у навколишнє середовище, на вітчизняних металургійних підприємствах сьогодні використовують різні очисні системи мокрого і сухого способів очищення, однак часто достатньо застарілих конструкцій. Термін експлуатації газоочисного обладнання на багатьох металургійних заводах країни давно минув, і становить 30-40 років.
Проведення ремонтів на діючих газоочисних установках не завжди виправдано, оскільки не дозволяє забезпечити достатньо високі сучасні вимоги до очищення промислових викидів.
Розвиток газоочисних технологій в останні роки дозволяє застосовувати переважно високоефективні пиловловлювачі. У першу чергу, це рукавні фільтри, потім електрофільтри і мокрі пиловловлювачі (скрубери Вентурі). В даний час провідне становище займають рукавні фільтри. При збільшенні коефіцієнта пиловловлення від 98 до 99% вартість електрофільров значно зростає (приблизно на 20%), а у мокрих пиловловлювачів ціна обладнання залишається незмінною, зате різко зростає кількість споживаної електроенергії. У той же час, вартість і споживаний обсяг енергії рукавних фільтрів з збільшенням ефективності пиловловлювання не змінюються, що робить їх найбільш привабливими з точки зору експлуатації.
Використання мокрих способів уловлювання пилу, зокрема, скруберів Вентурі, характеризується не тільки великими енергетичними витратами, але й наявністю стоків, необхідністю захисту апаратури від корозії та усунення відкладень на стінках апаратів і трубопроводів, а також необхідністю створення оборотних систем подачі води в пиловловлювач. Розмір часток, що уловлюються в скрубберах, складає від 0.2 мкм і вище. Ступінь очищення може досягати 96-98%, питома витрата зрошуваної рідини знаходиться в межах 0.5-6 л / куб. м, що обумовлює необхідність великого перепаду тиску (10-20 кПа) і, як наслідок, значних витрат на очищення газу.
Серед поширених сухих способів очищення промислових газів від пилу найбільша ефективність уловлювання тонкодисперсних часток (до 5 мкм) досягається практично тільки при використанні рукавних фільтрів і електрофільтрів.
Установки пиловловлення із застосуванням електрофільтрів характеризуються меншим енергоспоживанням, але для їх спорудження потрібні значні капітальні витрати. При цьому, електрофільтри чутливі до параметрів газів, що очищаються, при їх коливанні може знижуватися ефективність апаратів.
Електрофільтри застосовуються при температурах газів до 300-4000С і є найбільш економічними при обсягах газів більше 500 тис. куб. м / ч. У той же час, фахівці не рекомендують застосовувати електрофільтри при необхідності отримання запиленості газу на виході менш 500-100 мг / куб. м. Ступінь очищення газів досягає 98%. При використанні електрофільтрів пред`являються досить високі вимоги безпеки, оскільки велика ймовірність ураження працівників електрострумом у разі недотримання вимог охорони праці при їх експлуатації. Тому рукавні фільтри тут мають певну перевагу перед електрофільтрами.
При використанні рукавних фільтрів забезпечується залишкова запиленість нижче 5-10 мг / куб. м незалежно від властивостей вловлюється пилу; робота проводиться в широкому діапазоні очищуваного газу. Ступінь очищення становить 99% і більше, особливо пилу з високим електричним опором, уловлювання якої в електрофільтрах відбувається недостатньо повно. Витрата енергії становить 2-2.5 кВт / год на 1000 куб. м газів, що очищаються. Низькі капітальні витрати і помірні експлуатаційні витрати - ще один плюс таких пристроїв. Застосування синтетичних тканин в якості фільтрувальних матеріалів для фільтрів дозволяє використовувати їх при температурах вище 1400С. При цьому, такі тканини більше довговічні в порівнянні з натуральними вовняними і бавовняними тканинами.
Особливий інтерес представляють рукавні фільтри з імпульсною продувкою. Вони застосовуються для очищення газів обсягом 500 тис. куб м і більше та температурах близько 1500С з використанням синтетичних фільтрувальних матеріалів, що забезпечує високу ступінь очищення при значних питомих навантаженнях (4-6 куб. М / кВ. М * хв). Іншими перевагами таких фільтрів є відсутність рухомих частин, простота обслуговування, надійність дії і тривалий термін служби рукавів (до 20-24 місяців).
Що використовується
На українських метпідприємствах при модернізації виробництв сьогодні найчастіше встановлюють електрофільтри, рідше - рукавні фільтри.
Вважається, що початок процесу постійного зменшення забруднюючих речовин в металургії України було покладено більше 20 років тому - в 1987 році. Тоді на `Криворіжсталі` на ще діяла доменної печі № 4 були встановлені перші електрофільтри замість неефективних батарейних циклонів. На той момент це було справді революційне досягнення, і досвід `Криворіжсталі` стали переймати інші підприємства країни. У 1989 році на доменній печі № 6 батарейні циклони замінили на мокру аспірацію з трубами Вентурі. У 2003 році на мокрий спосіб очищення перейшли і на доменній печі № 5. Сьогодні системи, які очищають викиди за принципом індукції, діють і на доменній печі № 9.
Проте в даний час екологічні вимоги зросли, і цих потужностей вже недостатньо, тому на всіх доменних печах підприємства планується тільки суха очищення пилегазосодержащіх викидів. Так, при реконструкції з модернізацією доменної печі № 8 в 2008 році аспіраційна система печі була замінена на нову - ефективну. За допомогою електрофільтру були локалізовані викиди забруднюючих речовин в атмосферу від неорганізованого джерела ливарного двору з ефективністю очищення до 99%. У планах значилася модернізація з установкою сучасних аспіраційних систем доменних печей № 6, 7 і 5.
За відомостями прес-служби ВАТ `Арселор Міттал Кривий Ріг`, в 2009-2010 роках, згідно з договором з ЗАТ `Альстом Пауер ставала` (м. Москва), були закуплені сучасні пилоочисного апарати - електрофільтри, які в даний момент зберігаються на підприємстві. Однак фільтри ще не встановлені. У 2011 році під час проведення капітального ремонту 1-го розряду доменної печі № 6 у доменному цеху № 1 заплановано виконати реконструкцію установок очищення газу від ливарного двору і підбункерних приміщення з встановленням фільтрів. Ефект від впровадження буде визначений після запуску печі в роботу і виведення печі на повну потужність.
Нова доменна піч № 5 на Єнакіївському металургійному заводі (введена в експлуатацію в 2007 році) також обладнана сучасною системою аспірації для бункерної естакади та ливарного двору. Очищення аспіраційних газів здійснюється двома електрофільтрами виробництва чеської компанії ZVVZ; запиленість на виході складає не більше 50 мг / куб. м. У будівництво нової доменної печі № 3 також закладено обладнання сучасної системи аспірації ливарного двору і бункерної естакади, яка дозволить знизити викиди в атмосферу до 50 мг / куб. м (приблизно на 40%). Очищення аспіраційних газів буде проводитися аналогічними сучасними електрофільтрами.
При реконструкції у 2006 році доменної печі № 2 на МК `Азовсталь` була введена в експлуатацію система аспірації, що включає в себе електромагнітний фільтр, що значно знижує рівень запиленості газів (до 50 мг / куб. М). В даний час створюється електрофільтром магнітний шар не тільки знижує щорічні викиди пилу в атмосферу на 600 т, а й, утримуючи залізну пил, дозволяє пускати її назад у виробництво. У найближчому майбутньому `Азовсталь` планує обладнати подібними системами аспірації всі доменні печі.
Аспіраційна установка в комплекті з рукавним фільтром вперше в Україні була змонтована в 2000 році на доменній печі № 3 ВАТ `Запоріжсталь`. Система дозволяє вловлювати пилові викиди при виробництві чавуну з ефективністю 99,5%. Виконання заходу дозволило знизити викиди пилу в атмосферу на 4200 т / рік. Пізніше аналогічна система була встановлена і на доменній печі № 2. У вересні 2007 року на підприємстві була введена в експлуатацію аспіраційна установка (два електрофільтри) очищення викидів хвостових частин агломашин. Уловлювання і повернення у виробництво агломераційної пилу складає близько 2500 т.
ВАТ `ДМЗ` і ЗАТ `Донецьксталь` - металургійний завод `також щорічно виділяють значні кошти на охорону навколишнього середовища і реалізацію природоохоронних заходів. Так, завдяки обладнанню ливарного двору введеної в експлуатацію в 2007 році доменної печі № 1, а також доменної печі № 2 системою газоочистки з рукавним фільтром скорочення обсягу викидів шкідливих речовин в атмосферу склало за 2009 рік близько 1500 т.
На `ММК ім. Ілліча `в найближчому майбутньому також планується реконструкція газоочисток за агломашин № 2 і 3 з установкою електрофільтрів замість існуючих морально і фізично застарілих батарейних циклів. Передбачається, що вміст пилу в димових газах після реконструкції газоочисток не перевищить нормативної величини - 50 мг / куб. м. Викиди пилу в атмосферу, при цьому, знизяться на 4250 т / рік.
Ольга Фоміна
http://www.rusmet.ru/
Хроніка оновлення газоочисного обладнання на українських сталеливарних підприємствах
+380 44 237 XX XX +380 44 237 2567
Ідентифікатор: 8440
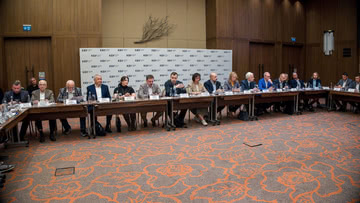
3 жовт. 2024 р.
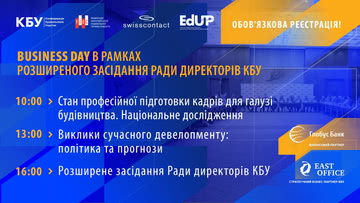
30 вер. 2024 р.